The Best Strategy To Use For Volution Bearing
The Best Strategy To Use For Volution Bearing
Blog Article
Some Known Facts About Volution Bearing.
Table of ContentsTop Guidelines Of Volution BearingA Biased View of Volution BearingThe Volution Bearing DiariesVolution Bearing - Questions
This is the amount of time that a team of apparently similar bearings will complete or go beyond before the development of a tiredness spall.This estimation can be somewhat complicated as it depends upon the relative sizes of the radial and thrust lots per various other and the contact angle developed by the bearing. It would be also challenging to reveal all the approaches of calculating P for all the bearing types shown. For conical roller bearings, the "K" drive factor is employed.
Radial cylindrical roller bearings that have opposing flanges on their inner and outer races have a restricted capacity of taking a thrust load though the length of the rollers. It is so restricted that we do not suggest customers deliberately do this. Appropriate drive loading is making use of roller ends and flanges for intermittent thrust and finding objectives.
Numerous applications do not run at a constant tons or speed, and to select bearings for a certain score life in hours based upon the most awful operating problem might show expensive (https://www.pubpub.org/user/jason-brown-3). Typically, a responsibility cycle can be defined for the different operating problems (load and speed) and the percentage of time at each
Volution Bearing for Dummies
In such circumstances, a complete task cycle takes place within one transformation of the bearing. In addition, the two examples can be incorporated for a number of awaited operating problems with reciprocating motion and various optimal loads and speeds. Determining the score life when tons and speeds vary entails initial calculating the L10 rating life at each operating condition of the responsibility cycle.
T1, T2, Tn = percent of time at various conditions, expressed as a decimal T1 + T2 + Tn = 1 Lp1, Lp2, Lpn = Life in hours for each and every duration of constant load and speed When a bearing does not make a full turning yet oscillates back and forth in operation, a lower equivalent radial load can be calculated using the formula below: Pe = Po x (/ 90)1/e where: Pe = comparable vibrant radial lots Po = real oscillating radial load = angle of oscillation, in degrees e = 10/3 (Roller Bearings) 3.0(Sphere Brgs) Some applications create extremely high radial and drive tons, and it may not be literally feasible or viable to use a single bearing that can taking both sorts of load.
When this happens, the device designer have to be mindful to make certain that the radial bearing takes just the radial tons, and the thrust bearing takes just the drive tons. A good method to accomplish this is to make use of a round roller bearing with one straight race at the "radial" place, as this bearing can not take any drive.
One method to accomplish this is to make the fit of the external races extremely loose in their housings: normally.5 mm/.020 In. to 1.0 mm/.040 In. Life modification factors allow the initial devices producer to better predict the real life span and reliability of bearings that you select and install in your equipment.
Some Known Factual Statements About Volution Bearing
Life modification variables, a1, a2 and a3, can theoretically be better or less than 1. manufacturing.0, depending upon their evaluation. In the OEM's process of forecasting the service dependability of his/her tools, it is sometimes needed to increase the dependability of the chosen bearings to predict a much longer imply time in between failings
If a reduced worth for L10 is calculated with an a1 element, and it is not appropriate, after that a bearing with greater Dynamic Capability needs to be picked. Dependability - % Ln a1 aspect 90 L10 1.00 95 L5 0.64 96L4 0.55 97 L6 0.47 98 L2 0.37 99 L1 0.25 There have been lots of improvements in bearing design and manufacture for many years that have actually been proven in life tests that result in enhanced L10 score life.
Several bearing applications are much from laboratory conditions. It can be challenging to validate an a3 variable greater than 1.0. Conditions such as heat, contamination, exterior vibration, etc will cause an a3 aspect much less than 1. If the lubrication transcends and the operating speed high sufficient, a considerably enhanced lube film can develop between the bearing's inner call surface areas validating an a3 aspect more than 1.0.
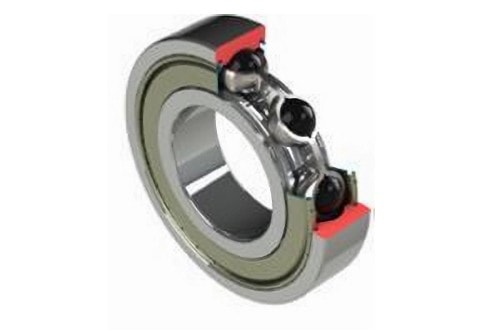
Not known Incorrect Statements About Volution Bearing
The following formula is used to calculate the System Rating Life: L10sys = (L1-w + L2-w + Ln-w)-1/ w where L10sys check over here = ranking life for the system of bearings L1, L2, Ln = score life for the private bearings in the system w = 10/9 for sphere bearings and w = 9/8 for roller bearings It has been gained from experience that bearings need a minimum used load to insure traction for the moving aspects so they roll as the shaft starts to revolve. https://forums.hostsearch.com/member.php?260201-volutionbearing.

Report this page